View Solutions for Your Business Here!
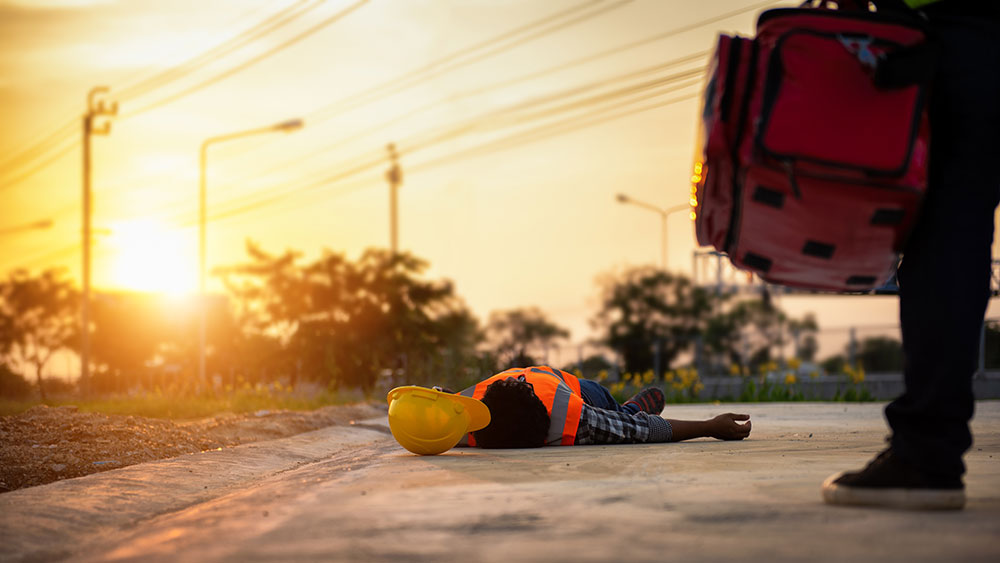
Your Safety Management Plan and the Methods That Make it Work
A safety management plan is only effective when workers comply with it. How can we help workers follow management plan template directions?
We'll look at one fatal incident, as well as a variety of actions that help manage the tension between accuracy in method and people-oriented problems. We'll also profile our Occupational Safety Solutions Safety Management Plan.
We hope this is helpful and even a little outside the predictable. We're always on the lookout for the 'significant extras' that give our customers an edge.
More specifically, we’ll look at:
- A tragic safety screw-up,
- The way perspective (or paradigm) influences safety management,
- The contribution of technical accuracy,
- The importance of the people factor, and
- A quick reminder of your digital options.
A Safety Screw-Up
In November 2019, Concorp Group Pty Ltd (now under external administration) was found guilty of failing to maintain a safe working environment and failing to provide instruction. A combined $650,000 fine was applied.
A 54-year-old worker fell 12 metres to the ground and died when the cantilevered platform he was working on overturned. Constructed two days earlier, the platform was boarded up by a supervisor who had concerns, but poor communication led to other workers entering the shaft and using the platform. Due to a variety of methodological errors, that worker fell to his death.
In this methodological failure, the platform was deficient, the risk assessment and incident response were incomplete, and the communication was horrendous. Julie Nielsen, from Worksafe Victoria, said, "This death could have easily been avoided if other workers had been warned … or if the company had pursued readily available and cheap modifications."
What an appalling tragedy! The safety plan was either poorly designed or inadequately implemented.
Paradigm Awareness and Your Safety Management Plan
Did paradigms come into play? I suspect they did. A paradigm is a collection of assumptions, concepts, outlooks, and practices that a person has. We all carry with us a variety of paradigms that we use in different locations and situations. Let’s look at an example we can probably all appreciate.
Consider for a moment Allan, Barry and Charleen who use the same particular stretch of local road. Allan believes this stretch has been marked at 50km/h so the Highway Patrol can make money. Barry sees the same speed limit as annoying, but also considers it a necessary evil that will save lives. Charleen, on the other hand, who's been infringed three times on that same road, only sees the 'mongrel-bastards' that are out to get her. Charleen doesn't even have an opinion on the speed limit - her status as a victim of the Highway patrol is all she can see.
When Allan, Barry and Charleen approach that stretch of road, they do so very differently.
- Allan is angry. Once he gets free of this 'speed trap' he'll do the rest of his trip at 20km/h above, justifying it to himself, because he's been slowed down by money-clutching politicians.
- Barry is annoyed, but also safety conscious and compliant. He will probably continue driving in that same attitude throughout his journey.
- Charleen, however, is dysfunctionally aggressive. As she drives on that road, she's tapping into her hatred of those 'mongrel cops'. They caused her to lose her license for a month. She checks her rear vision for the fifth time, and then focuses her attention 200 metres ahead, where she sees a white car parked behind a tree. "Is that a cop?" she wonders. She fails to see the soccer ball roll across the road 15 metres in front of her. She also doesn't see the eight-year-old boy who, a moment later, chases that same ball.
That’s the importance of paradigm.
We also view safety management according to our paradigms - and we apply different versions to different situations. We all know workers who are careful in some areas of safety, but less so in others. It’s wise to stay aware.
Personal preferences and dislikes most definitely impact safety management. For safety management to work at it’s best, it’s worth getting into the head of everyone involved.
Consider these ‘paradigm’ suggestions:
- Talk up safety management as a head-game. Creating a paradigm-aware work culture.
- Communicate and model useful paradigms to influence the way others see safety.
- Ensure all your leadership is onboard. If they doubt it, have that conversation.
- Be alert for stinking thinking, and address as a matter of urgency.
- Identify your paradigms, and
- Encourage your team to do the same.
Every OSS safety template is designed to minimise the impact of paradigm, but only you can accommodate the inherent individual aspects of you and your workers.
A Management Plan Template Needs Technical Excellence
It's also essential to plan for and fulfil, all legislative requirements. Your safety documents must incorporate all required items, and also empower your record-keeping and evidence of compliance.
A good management plan template will meet the requirements of legislation and regulation, while also addressing the needs of the people using the resources.
For example, to return to the tragic example given earlier, Worksafe Victoria stipulates the following five steps to prevent work platform falls when working with formwork:
- Competence in Design: A competent person must design the platform, and it must be capable of supporting the expected loads.
- Formal Sign-Off: There must be a system involving an official sign off as structurally sound before anyone uses the platform.
- Training: Site-specific training must address onsite risks associated with formwork decks.
- SWMS: A Safe Work Method Statement for High-Risk Construction Work must be prepared and followed.
- Fall arrest: A catch platform, safety nets or equivalent system must be in place.
Do your WHS documents address these criteria? Do your individual management plan template items do this? It's hard to know sometimes, which is why choosing a thoroughly professional supplier is so important.
Occupational Safety Solutions is a proven supplier of technical excellence.
When a Safety Management Plan Really Cares
When we talk about care, we're not suggesting team hugs, heartfelt conversations or 'feel good' notes of appreciation discretely left for your workers to find. We're talking about words and deeds that show the business' leaders genuinely care about the safety of their workers.
Leading with personal care means genuinely prioritising the welfare and wellness of your workers. There was a supervisor who closed off that fatal platform. Clearly, at that point, there was genuine care. Methodological failure followed, however: repairs were not made, communication was totally inadequate, and later workers didn't assess the risks correctly when they engaged the platform back into service.
Was there a lack of care at a management level? What about at a worker level?
Here are some ways you can demonstrate your care:
- Be interested in your team as people, not just as units of production.
- Don’t pretend. Insincerity exposed is like plastic surgery gone wrong; the ‘ugly’ factor to our reputation can be impossible to repair.
- Be patient, because Aussies are sceptical. It might take a while before they take your care seriously.
- Publicly appreciate safe work practice. Verbalising appreciation within the earshot of others makes a difference.
- Demonstrate your care intermittently; i.e. not every time, or in a predictable way. This produces the best results.
- Work out what it looks like for you. Showing care looks different for every leader.
- Talk about this topic with peers to generate good ideas and priorities.
Regarding Digital Options
The best of efforts won't remove all administrative pain, lost paperwork, audit angst or worker laziness. This is why we teamed up with Safetyminder software. After working with them for a number of months, we introduced you to them in November 2018. You can read that article here. There’s also a 1-minute introduction video and here’s a direct link to their website.
If you invest in their service, you'll discover their software is:
- Convenient,
- Sends reminders,
- Removes excuses, and
- Reduces administrative loads.
Also - and this is a biggie - the Safetyminder software has been designed around our WHS Management System, which means WHS templates purchased from us will integrate seamlessly and comprehensively!
Some Safety Management Plan Options
Our Safety Management Plan templates provide structure and supporting documents to make your work as easy as it can be. Each plan provides a framework around which a project-specific can be built. They address generic Work Health and Safety (WHS) legislation and regulatory needs, and also more specific inclusions according to need (e.g. environment, asbestos, etc.).
Each plan template indicates where business and site-specific information is required, and also includes supportive guidance notes.
We provide Safety Management Plans for:
- Work Health and Safety (generic)
- Asbestos Management
- Environmental Management
- Quality Management, and
- Health, Safety and Environment (HSE) Management (combines WHS Management Plan and Environmental Management Plan)
- Project Management (combines WHS Management Plan, Environmental Management Plan and Quality Management Plan)
As with almost all our templates, these safety management plan templates are:
- Available for instant download,
- Fully editable in MS Word format,
- Supported with guidance notes, and
- Include a comprehensive range of resources, tools and schedules, and
- Are supported by a two-year and (usually) complimentary ‘update and replace’ service
The Wrap on Method
We've identified that a safety management plan only works when workers follow the method steps provided, and when those steps are technically correct. We've considered the tragic death of a 54-year-old worker in Victoria. We've also discussed how paradigm, technical excellence and genuine care can produce better safety outcomes. Finally, we looked at our Occupational Safety Solutions Safety Management Plan.
We hope this has been helpful.
We care about the Allans, Barries, and Charleens. We also care about the 8-year-olds who are kicking a ball around, waiting for a parent to come home. Paradigm awareness and genuine care contribute to our technical excellence.
If you’d like to know more about our WHS (safety) management plan options, or if you would like a tailored safety solution, you can pursue the links shown above, call 1800 304 336 or Request a Callback.