View Solutions for Your Business Here!
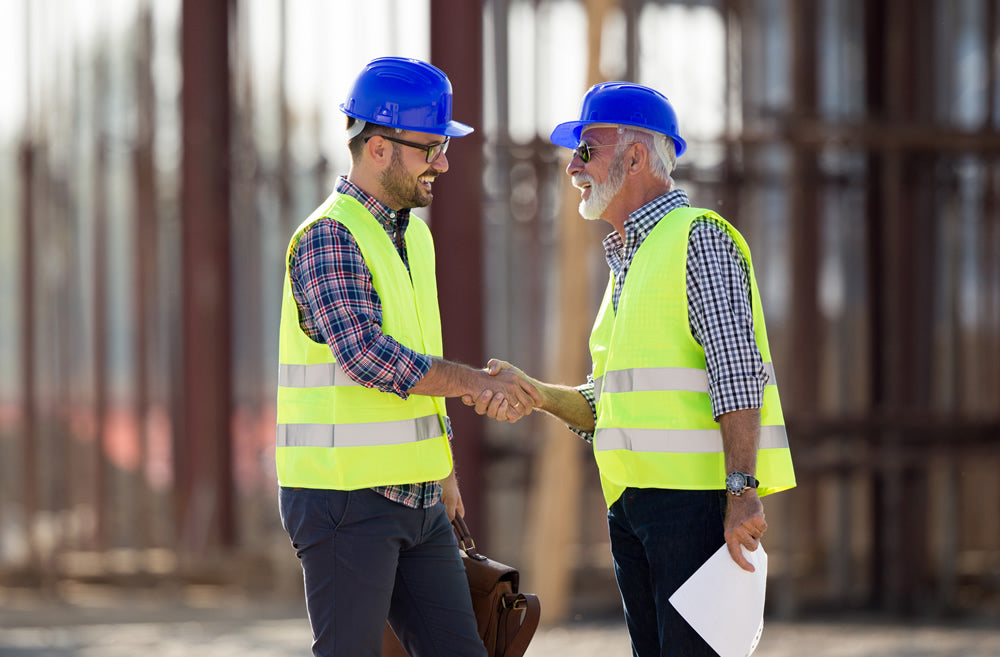
Win Your Building and Construction Tender
You’re in the business of winning. We’re in the business of helping you win! This article looks at WHS Management Systems, their parts and inclusions, aspects of tendering and pre-qualification certification, as well as tactics and tools to help you do it well.
Tendering can be exhausting and overwhelming - when you do it on your own. We encourage you to grab a guide for the journey.
We’ll begin by answering some relevant questions; some are common, some might surprise you. We’ll then work through the elements of a WHS Management System. Obviously, we hope you’ll decide to purchase one of our pre-designed systems; but even if you don’t, we hope this article proves to be a powerful resource that equips you to tender successfully.
We want you to avoid ‘tender’ pain, so you can soak in the pleasure of winning.
Common Questions About WHS Management Systems
Here at Occupational Safety Solutions we receive a huge range of questions. Customers ask questions about our business, the WHS/OHS industry, our resources, and the way these should be used as they prepare their Response to Tender document.
These questions are common:
- What’s the difference between a Management System and a Management Plan?
- Is a Template Solution really that helpful?
- Are Occupational Safety Solutions systems compliant with AS/NZS 4801?
- What about ISO 45001?
- Are Occupational Safety Solution systems third-party certified?
Let’s address these concerns.
Management System or a Management Plan? What’s the Difference?
Sadly, the language is a bit confusing: “systems” are global for your business and apply pretty much anywhere you work, “plans” on the other hand are site-specific and/or job specific.
This article focuses on WHS Management SYSTEMS, not WHS Management Plans.
Also, a WHS Management Plan (WHSMP) is not always required, but when it is requested, it is a highly focused document. Your Management Plan can address issues relating to WHS, HSE, asbestos, environmental, quality, project planning, or a combination of these.
If you do need a WHS Management PLAN, then follow this link. You’ll find a free e-book empowering you if you want to go it alone. This resource addresses aspects of purpose, currency, the five critical questions of template design and overarching OHS/WHS template design principles.
If you’d rather benefit from these principles already applied, on the same page you’ll also find our already prepared Management Plan templates.
Is a Template Solution Really That Helpful?
You’re reading the article, so you obviously want to win. You can’t avoid creating a system and documentation, so your options are essentially:
- Purchase a template solution, or
- Create your own.
If you ALREADY know you want to invest in pre-prepared WHS Management System template, this link will take you to the generic package, as well as 23 industry specific packages (with a comprehensive set of industry specific SWMS’s included).
Creating Your Own
You may want to create your own system. The main allure of this approach is to presumably create something unique to reflect your enterprise, or to develop a skill set in an employee to better position yourself for future tender processes.
On the surface, this can look like a wise approach. There are problems however. Consider that buyers, Safety Officers, contractors and staff are used to dealing with conventional documents, registers and tools. You might create something that improves functionality and aesthetics, but human beings generally don’t like change and innovation; it causes extra effort, delays and hesitation. When you’re manoeuvring for a win, none of this is good!
Going solo will be a significant undertaking, but if you do, the information in the rest of this article will prove helpful. While you’re deciding, factor in that you will need to:
- Gain a significant amount of necessary knowledge and skills,
- Design a large array of policies, forms and registers,
- Invest many days and weeks in the process, and
- Spend significant money.
Purchasing a Template
There is an alternative. You can purchase either a generic management system, or an industry specific one. There is a significant difference in your investment for each, however the package inclusions are also significantly different.
The generic management system addresses the same topics and resource issues as the industry specific one. What differs is that the industry specific package has been fine tuned with that specific industry in mind.
Both packages will save you money, and when you purchase the industry-specific option this becomes a significant amount. These tailored solutions deliver four immediate advantages:
- You save countless hours due to the specificity of the documents.
- You receive an exhaustive range of relevant Safe Work Method Statement (SWMS) templates.
- You save financially (significantly so) against the price of purchasing items separately.
- They’re templates. You can use them again and again.
We’ve done the hard work, the price we charge is fair, everything is designed to provide a significant saving, and if something changes in the legislation or regulations, we’ll let you know. Essentially, the guesswork is removed and the savings are tangible.
If you would like to purchase or investigate further, this link will take you where you want to go.
Are Occupational Safety Solutions Systems Compliant with AS/NZS 4801?
Yes! All our WHS Management Systems are compliant with, and can be certified against, AS/NZS 4801.
If you would like to learn more about the AS/NZS 4801 standard, you can visit Standards Australia. If you’d like to purchase a copy of the standard, you’ll find it at Intertek Inform (previously SAI Global).
What About ISO 45001?
The International Standard ISO 45001 was published in early 2018. Unfortunately, a number of players in the safety industry have been leveraging the confusion it caused. We believe this is inappropriate and we won’t be doing this to you.
Questions are being raised about how and when Australia should comply with this ISO standard. Standards Australia hasn’t finished evaluating it against AS/NZS 4801, there are significant legislative issues at play, and perhaps most significantly, these things rarely happen quickly. .
For all these reasons, the smart money says change is still a ways off.
Are Occupational Safety Solution Systems Third-Party Certified?
This is a fair question, and the answer might surprise: our systems are not third party certified. They can’t be! WHS Management Systems can only be certified WHEN APPLIED TO a particular organisation. You have to implement the system, use it on your projects and then you can have it third party certified.
It’s like an Armani suit. Wear it correctly and you’ll look awesome - but only if you wear it right. A certifier will let you know if you’re ‘wearing’ your WHS Management System correctly. We’re also happy to give you some ‘grooming tips’.
If you apply the systems correctly, you will get certified.
Questions Specific to the Tender Process
We are also asked questions regarding the tendering process. More specifically we are asked two specific questions again and again:
- How do I answer, “Do You Have a Third-Party Certified WHS Management System?”
- How do I answer, “Is your WHS Management System compliant with AS/NZS 4801?”
Let’s answer these for you.
Is Your WHS Management System Compliant with AS/NZS 4801?
If you’re using an Occupational Safety Solutions template, and you’re doing the necessary due diligence in applying it, you can confidently answer “Yes”!
All our WHS Management Systems are compliant with, and can be certified against, AS/NZS 4801.
If you would like to learn more about the AS/NZS 4801 standard and currency, you can visit Standards Australia. If you’d like to purchase a copy of the standard, you’ll find it at Intertek Inform (previously SAI Global).
Do You Have a Third-Party Certified WHS Management System?
This question can put you off. Perhaps it’s even designed that way. Here’s a simple but profound tip: ask!
In our experience, a vast number of projects do NOT require you to have third-party certification. The question is often included as part of a proforma presentation, third-party certification is often not a project specific requirement.
We advise you to ring the tender contact and ask the question. Is it really necessary? You might be surprised. If not, you’ll be right to proceed.
If it does require certification, remember you must implement the system before being assessed and have evidence of its use in past projects. There is an abundance of providers who are capable of doing so. Just Google!
As already stated, our WHS Management Systems are fully compliant with required standards, and also follow industry guidelines and conventions.
Essential Elements of a WHS Management System
WHS management systems follow a relatively standardised format. The focus areas are consistent across industries; document specifics and sub-categories are not. The five focus areas are:
Part A - Introduction (Global Overview Documents)
Part B - Training and Supervision
Part C - Risk Management
Part D - Incident and Injury Management
Part E - Record, Review and Improve
In the following paragraphs we will discuss the parts and components contained in each focus area. If you already know you want to invest in a template this link will take you where you want to go.
Part A - Introduction (Global Overview Documents)
The introductory part of your WHS Management System needs to include a variety of global oversight policy and compliance documents.
It should include the following policy documents:
- Work Health and Safety (WHS) Policy
- Workplace Consultation Policy
- Equal Employment Opportunity (EEO) Policy
It should also include documents that explain policy processes and demonstrate compliance. A standard way of doing this is by providing:
- A Roles and Responsibilities Register, and
- An Organisation Chart
Part B - Training and Supervision
Your training and supervision standards will be under the microscope. Ultimately, you need to show that your policies, plans, registers, agreements and practices work together in a way that supports your overarching WHS policies.
There are three main areas to address in training and supervision:
- Your training and competency standards.
- Your training and competency methods.
- Your WHS and company induction procedures.
In other words, you need to answer these questions:
- What training will you provide?
- How will you do this?
- How will you prove your system works?
To answer these questions, you’ll need documents that clearly demonstrate your aims and methods. You’ll also need to prove you followed through. To do this, ensure your system includes a:
- Training and Competency Policy,
- Training Plan, and
- Policy Agreement (for your staff and subcontractors to sign).
With these in place, you will then require appropriate registers in place to guide and record your training and supervision processes.
- Training Register
- Skills and Competency Register
- Worker Information and Induction Checklist
- Site Safety Induction Register
- Medical Register-Worker
- Subcontractor or Visitor Attendance Register
Part C - Risk Management
Risk management is the most significant focus area we need to address, but we’ve massively reduced the complexity, technical issues, cost and effort.
There are 18 broadly recognised compliance areas and 65 policies, plans or documents to provide. The 18 areas include:
- Hazard Reporting and Risk Management
- Safe Work Method Statements (SWMS)
- Live Work
- Site Safety
- Subcontractor Management
- Fire and Emergency Procedures
- Hazardous Substances
- Personal Protective Equipment (PPE)
- Company Plant, Equipment, Tools and Vehicles
- Manual Handling
- Purchasing
- Environmental
- Noise
- Remote or Isolated Work
- Shift work
- Stress and Fatigue
- Alcohol and Drugs
- Internet, Email and Mobile Phones
There is little value in making specific comments on all 65 of these necessary resources, and listing them would be a lengthy and perhaps pointless exercise. Instead, we will simply group them by type and list them in paragraph form. This way, if you want the detail you can read on, and if not, you can skim over that section easily.
There are 14 policy documents. These include policies on live work, hazardous substances, personal protective equipment (PPE), plant and equipment, manual handling, purchasing, site environmental, noise, shift work, stress and fatigue, drug and alcohol, smoke-free workplace, internet and email, as well as mobile phone use.
There are 5 plan documents. There is a risk treatment plan, risk action plan, site safety management plan, waste management plan, plus a fire and emergency response plan.
There are 10 process, procedure, guideline or rule documents. These pertain to the hazard reporting and risk assessment, risk management process, remote or isolated work, emergency procedures, risk management, purchasing, noise control, drugs and alcohol, PPE and site safety.
There are 15 thorough and time-proven checklists. These will significantly empower your proactive risk management in the areas of hazard identification, site safety forms, site safety, office / warehouse inspection, subcontractor safety, hazardous substances risk, plant and equipment hazards, vehicle inspections, manual handling, purchasing, site environmental issues, noise control, stress, fatigue, and finally, the responsible service of alcohol. If you were to create all these on your own, you might really need the last one!
There are 19 separate registers. These are critical to your compliance, aiding reference and proving compliance. These registers relate to your SWMS, RCD testing, key roles and responsibility, emergency information and contact numbers, electrical tagging, subcontractor, fire and emergency evacuations, fire safety training, fire fighting equipment maintenance, hazardous substances, safety data sheet (SDS), PPE (by company and worker), tools, plant and equipment (use, location and maintenance), equipment repair, vehicle maintenance and purchasing.
Of course you also receive our time-proven SWMS Template and Hazard Report Form.
Part D - Incident and Injury Management
If the unfortunate should happen, then you will need a variety of policies, procedures, registers, forms and a return to work program. This focus area of your WHS Management System is all about providing a response that protects your worker as well as your organisation.
This focus area has six subcategories and 14 policy or document resources. The subcategories are:
- Incident and Injury Management Procedures
- Incident and Injury Reporting
- Incident and Injury Review
- First Aid
- Workplace Violence and Bullying
- Disciplinary Procedures and Counselling
There are 3 policy documents. These relate to incident and injury management, workplace violence and bullying, and first-aid.
The 5 procedure documents relate to first-aid, workplace violence and bullying, disciplinary procedures and counselling, incident and injury management, and your return to work program.
There are 3 forms. These include two reporting forms in case of incident and injury, as well as traffic incidents. The final is an Incident and Injury Investigation Form.
Registers in this focus area cater to LTI (lost time injury), MTI (medical treatment injury) and incident and injury.
Part E - Record, Review and Improve
The final focus area addresses meetings, complaints, audits, performance, reviews and improvements.
- Meetings and Toolbox Talks
- Complaints and Corrective Action
- Audits
- Performance
- Document Control and Review
The tools provided will assist your:
- WHS meetings,
- Toolbox or pre-start talks,
- Non-conformance complaint and corrective procedures,
- WHS performance and legislative compliance, and
- Audit and review processes.
There are 16 procedures, guidelines, templates, checklists, registers or forms provided in this focus area.
Tendering Success
You’ve probably realised by now that there is a lot involved in your WHS Management System (WHSMS). If you’ve read this far, you’ve hopefully been empowered with a great deal of information. It’s also possible you’ve been overwhelmed! As we said at the beginning, both the tendering process and creating a WHS Management System (WHSMS) can be overwhelming - if you go it alone.
If you do choose to go it alone, follow whatever tips you can find, including the ones in the article.
If you’d rather get some help, invest in a WHSMS solution.
Let’s close out this article with four clarifications.
First, buyers and compliance officials search for key phrases, consistency in process, and compliance with established conventions. It is critical that you present the correct information, and that you present it the right way. This is not an area for creativity. If you do choose to invest in our WHSMS templates, you can be certain it will be loaded with the most effective terminology, content and formatting.
Second, remember that purchasing our templated WHS management systems does not remove all of your labour, but if you follow the templated guidelines, your workload will be massively reduced! We have done everything we can do. There is a customisation factor that only you can fulfil, but you will also find a great deal of assistance is provided by our resources.
Third, using Occupational Safety Solutions resources means you access highly specialised yet flexible resources. We know both the industry and the marketplace! We are fully tapped into the most current industry developments, we employ Continuous Improvement Systems, and we communicate with our clients. This is how we deliver quality.
Lastly, it is our firm conviction that our WHSMS package options provide innumerable benefits. You can purchase a generic package, or you can purchase an industry specific package (with industry-tailored content and an extensive range of SWMS resources included). Whatever you choose, it’ll be a no-lose investment in safety, efficiency, financial savings and perhaps that tender won!
If anything you’ve read here has stirred questions, a quick call to 1800 304 336 should see it answered. Call also if you’d like to know more about the WHS Management System, it’s supporting resources, and especially the combination savings available via the industry specific versions. If you’d rather go straight to the online options, this link will take you where you want to go.